Place of conducting the research: Indian Institute of Science, Bangalore
Mentor(s): Prof. Suresh Sundaram
Duration: Septembere 2019 - January 2020
Automatic guided vehicle (AGV) has been a kind of logistics transportation equipment being widely used in an automated factory. One of the most intriguing challenges in warehouse automation is the self-locking mechanism used to latch the automated guided vehicle (AGV) to the carts or trolleys.
What makes designing and modelling the docking system so intriguing is the constraints involved in the factory layout such as the factory floor material, inclinations, turning radius at junctions, payload in the cart, dynamic obstacles etc.
​
​


My research was primarily aimed to develop an economical docking system used in automating an in-factory transportation system of a specified automotive firm. It had to abide by some challenging constraints like,
-
1-metre lane width.
-
up to 5 degrees inclination angle.
-
Tight turning radius, 1-metre radius at few junctions.
-
Maximum payload of the cart up to 500 Kg.
Apart from the above constraints, the most demanding limitation was to design the docking system for pre-existing trolleys (figure above), which were already in use. Replacing all of these trolleys would be infeasible for the firm and developing an economical prototype of the self-locking mechanism which could importantly accommodate all the constraints was essential.
Below shows the images, simulated video of the lead screw based self-locking mechanism and its stress analysis. The lead screw-based mechanism is chosen primarily due to its load-carrying capacity. The camber on the latch is provided to increase the tolerance of precision for the docking system.
​
​

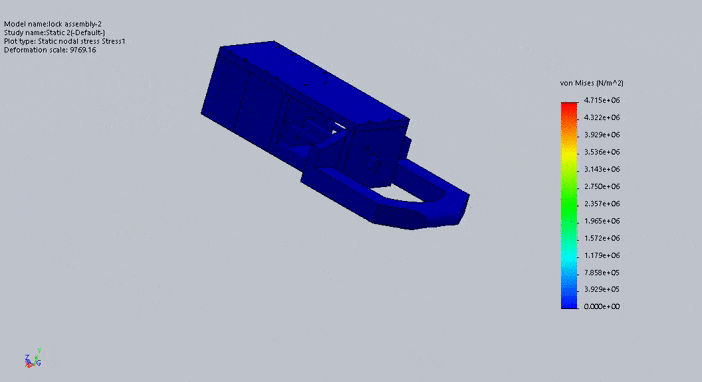